Thermopile pyranometer history
Since 1913, Kipp & Zonen had been manufacturing, for the measurement of thermal radiation and light, a fast and sensitive thermopile (made up of many thermocouples) designed by Dr. Moll of Utrecht University. However, it was not until a meteorological conference at Utrecht in 1923 that Dr. Moll drew the attention of scientists to this thermopile. Professor L. Gorczynski of the Polish Meteorological Institute decided to construct a pyrheliometer and a pyranometer using modified Moll-Gorczynski thermopiles.
Because of the thermopile characteristics the instruments could be small, light, low cost, have a continuous voltage output signal, and not require any external electrical power or control systems. These prototypes proved to be successful and Kipp & Zonen became the manufacturer of the instruments in 1924.
How the thermopile pyranometer works
The thermoelectric detection principle is used, whereby incoming radiation is almost completely absorbed by a horizontal blackened surface, over a very wide wavelength range. The resulting increase of temperature is measured via thermocouples connected in series or series-parallel to make a thermopile.
The active (hot) junctions are located beneath the blackened receiver surface and are heated by the radiation absorbed in the black coating. The passive (cold) junctions of the thermopile are in thermal contact with the pyranometer housing, which serves as a heat-sink. More recent, higher performance, pyranometers use a Peltier element. This is also thermoelectric, but the dissimilar metals of a thermocouple / thermopile are replaced by dissimilar semiconductors.
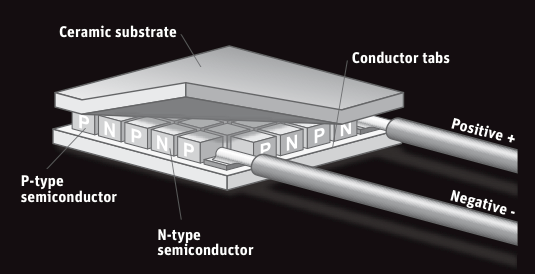
It is necessary to protect the black detector coating against external influences which may affect the measurement; such as precipitation, dirt and wind. Nearly all pyranometers use an optical quality glass for their hemispherical single or double domes.
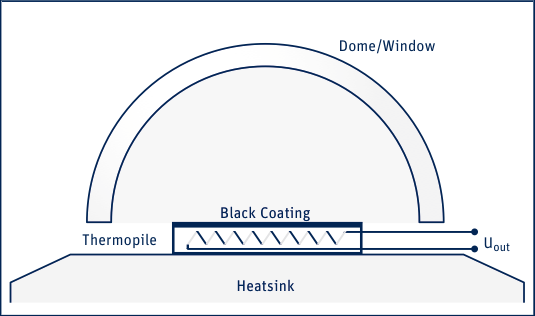
Depending upon the glass, the transmission is from 300 nm or less to about 3000 nm. Double domes give better stability under dynamically changing conditions by further ‘insulating’ the sensor surface from environmental effects such as wind and rapid temperature fluctuations.
The shape of the dome, and the refractive index of the material, improves the response of the sensor when the sun is close to the horizon, ‘bending’ the incoming radiation beam. The highest specification pyranometer available, our modelCMP 22 uses Quartz domes for a wider spectral response. The higher refractive index further improves the directional response and better thermal conductivity than glass provides other performance benefits.
Passive thermopile / Peltier pyranometers such as our CMP series do not require a power supply. The detector generates a small voltage in proportion to the temperature difference between the black absorbing surface and the instrument housing. This is of the order of 10 µV (microvolts) per W/m2, so on a sunny day the output will be around 10 mV (millivolts). Each pyranometer has a unique sensitivity, defined during the calibration process, which is used to convert the output signal in microvolts into global irradiance in W/m2.
Our SMP range of Smart pyranometers have the same detectors as the equivalent CMP models but with built-in digital signal processing and performance enhancement, and therefore they require external power to operate.
To maintain performance, recalibration is usually recommended every two years, and a high quality water-proof connector for the signal cable greatly simplifies the process.